Bakery Biz, September-October, 2021
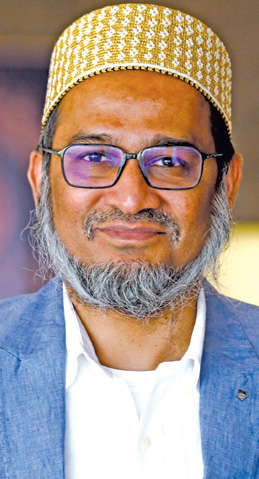
YUSUF
PATANWALA
FOUNDER
AND CEO
AUTOBAKE PRODUCTIONS
We have been talking about excellence in manufacturing through the twin principles of Quality and Productivity through our last three articles. Now if you need any inspiration to kick start your journey in this direction, then look no further. Here, in the below quote and the story that follows, you will witness an example of a visionary leader who pioneered the concept of McDonaldization of Eye-Care in India to become a benchmark for world class and yet affordable health care system in India and the whole world.
Dr. Venkataswamy (endearingly known as Dr. V in an interview to the Fast Company quipped:
“If Coca-Cola can sell billions of sodas and McDonald’s can sell billions of burgers, why can’t Aravind sell millions of sight-restoring operations, and, eventually, the belief in human perfection?” Dr. V had a vision – to restore the gift of sight to millions of poor blind people through the Aravind Eye – Care system. Aravind’s business model is basedon his vision to solve the blindness problem regardless of the patient’s ability to pay. Aravind has been able to successfully execute this business model over the last forty years to become the largest provider of eye-care services in the world.
A lot of reading material is available on the web regarding the Aravinda Business Model including those written by McKinsey and The Harvard Business School. Let us extract and discuss points that are relevant to us in the manufacturing context
While we discuss the Aravinda Case Study – let us get the facts straight right away:
- They perform more than 400,000 surgeries every year
- 60 per cent of them are performed totally free of cost
- The quality standards are comparable to that of the best hospitals in the UK
- They make a very decent profit, fund their own growth, and
- They have sustained this performance consistently for the last 40 years!!
HOW IS IT DONE?
The answer lies in their core strategy which they call as McDonaldization of Eye Care or in other words an assembly line approach to servicing eye care that helps them reduce their costs and increase their productivity by TEN times!!
The assembly line concept is based on the three basic principle of Lean, Balance & Flow. Let’s understand each one of them in a little more detail: The concept of lean is all about reaching a stage where we use minimum labor, space, time and material to achieve the maximum output or results. The lean concept encourages us to relook at all our business or manufacturing processes with a fresh approach. We may be operating in a certain way, adopting particular methods and following a set of processes over a long period of time. However, over those same years the people may have changed, technology might have become obsolete and customer expectations could have undergone a drastic change. These consistently small changes over a long period of time have the power to completely disrupt existing businesses. Hence the basic principle of Lean Management – to question the purpose of each and every process!
Many practitioners of lean management were surprised to find out how so many of their existing processes and systems had become outdated and they were completely unaware of them! Moreover, they kept spending expensive resources on obsolete processes and systems for so many years.
So, let’s look at some of the good practices that could help us to become a Lean Organization.
Manpower: What did Aravinda Eye Care do in respect of their most expensive resource – the Eye Surgeons? They ‘focused’ on the main skill of the eye surgeon i.e., to operate the patient. All activities that did not involve ‘operating on the patient’ were taken away from the surgeon and given to the well-trained operating nurses. Just by differentiating the high skill activities from the low skill activities,
Aravinda was able to maximise the productivity of their eye surgeons who now perform at least 10 times more surgeries in a given time period compared to any other eye surgeon in India or any developed nation across the world.
Result – the operating cost per eye surgery dropped dramatically and in return the volumes of eye surgeries performed by Aravinda increased multiple times.
What was the effect of the above system on the operating nurses – their skill level increased multifold. They got to perform tasks which they could have never expected to perform in a traditional setting. This led to high levels of motivation and job satisfaction. We all know how important these aspects are in boosting productivity! However, to reach this stage, Aravinda set up very detailed standard operating procedures and manuals backed up by continuous training and skill development. They kept learning (fast) due to the high volumes and improvised the system to such an extent that it became nearly error free.
Result – the standards of quality at Aravinda are today comparable to (and even exceed on many parameters) the best eye care facilities in developed nations.
Space and Time: When workflow or the manufacturing processes are structured in an ‘assembly line like fashion’, the maximum benefits go to saving of precious time and space on the shop floor.
What did Aravinda do? They calculated, tabulated and analysed every step (with timings) right from the moment the patient entered the facility up to the time he /she left the premises. They studied and then designed the entire ‘flow’ in such a manner that there would be nothing but a seamless movement of the patient in the entire system. Based on the diagnosis and the procedure recommended by the diagnosis team, the patient was directed (in real time) in series of steps that resulted in the entire treatment being completed in a SINGLE VISIT! SICK patient entered the system from one end and exited from the other end completely CURED! Operating rooms are designed in such a manner that the surgeon can perform multiple operations without wasting precious time. Two operating beds next to each other in the same operating room – saving space! This is a result of meticulous planning and disciplined execution.
Results – we all know are high productivity, high quality at the lowest possible costs!
Material: Saving on material brings about major savings in the operating cost of any manufacturing company. What did the Eye Care Hospital do? They found the sutures used by the surgeons were utilised only upto 30 per cent of the entire length. The remaining 70 per cent was discarded. Thus, they go back to the suppliers – ask them to shorten the length and ultimately reduce costs!
They recycle wastes and use them creatively for various non-critical functions. They are frugal in spending money on activities that do not directly or indirectly affect the outcome or quality of any treatment. These fantastic and thoughtful initiatives on saving of manpower, space, time and material have been a bedrock on which many successful ventures have thrived. Negligence in these areas have led to a downfall of many a great initiatives in business today.
BALANCE: An Assembly Line is designed on the basic principle of Balance. When work flows through the line one process after another, it is natural that one activity needs more or less time, space or effort compared to the other activity in the sequence. For example, the mixing time for a particular batch of dough could be just three minutes but the next process in line i.e. the baking process would need 30 minutes. Ten times more time than the activity preceding it. The succeeding activity of cooling might be 90 minutes and packing again just 3 minutes. This scenario would vary from product to product and machine to machine. So, how do we balance the flow that is so important for production efficiency?
My answer is – this is exactly where the skill and talent of a smart production guy comes into picture. What will a smart production guy do? He/she will study and tabulate his/her findings in a format that would give a clear picture of what is happening on the shop floor. Identify gaps, re-allocate resources judiciously, eliminate wastes, improve performance, and inculcate discipline. What will this exercise result in? It will help free up resources tied up in non-value adding activities due to improper planning, increase plant capacity, save costs, and increase productivity!
End of the day – it’s all about balance!!
FLOW: A manufacturing activity or a shop floor does not work in isolation. I have seen many a top management work, focus and devote maximum time towards increasing sales (which is important but need to balance) only to hit a roadblock at later stages in terms of delayed deliveries, inconsistent quality, and high level of market complaints.
I have never achieved any major breakthrough success in manufacturing without ALIGNING the requirement of the final consumer with – the sales, the distribution, the logistics, the purchase, the stores, the maintenance, the quality control, the suppliers, the finance, the IT – all together on ONE PLATFOR M!
Yes, it is only when all various functions work together and align together as one that we can achieve breakthrough success in our businesses. Without this flow or alignment of each and everyone involved in business, every day is like firefighting or accepting mediocrity (rather than excellence) by maintaining status quo.
The Aravinda Story is quite inspirational, and I will highly recommend my readers to read and learn more on this topic from wherever possible. Hope you have enjoyed reading this brief article and found it inspirational enough to kick start ‘your’ journey in Manufacturing Excellence in your company itself!
To recap our previous articles, we have established the importance of manufacturing in the economy of any developing nation and how use of technology is the real game changer for any manufacturing company through our first article. In the second article, we laid the foundation by identifying and learning about the importance of 4Ms of Manufacturing. The third article dealt with the correct definitions and interpretation of Quality and Productivity.
In our upcoming article we will discuss innovation and how we can lay a foundation for building our own dream factory. Till that time, please be safe, take care and do not hesitate to get in touch with me anytime!